The British Royal Navy has named the newly-built Astute-class nuclear-powered submarine HMS Agamemnon. Doing so, the…
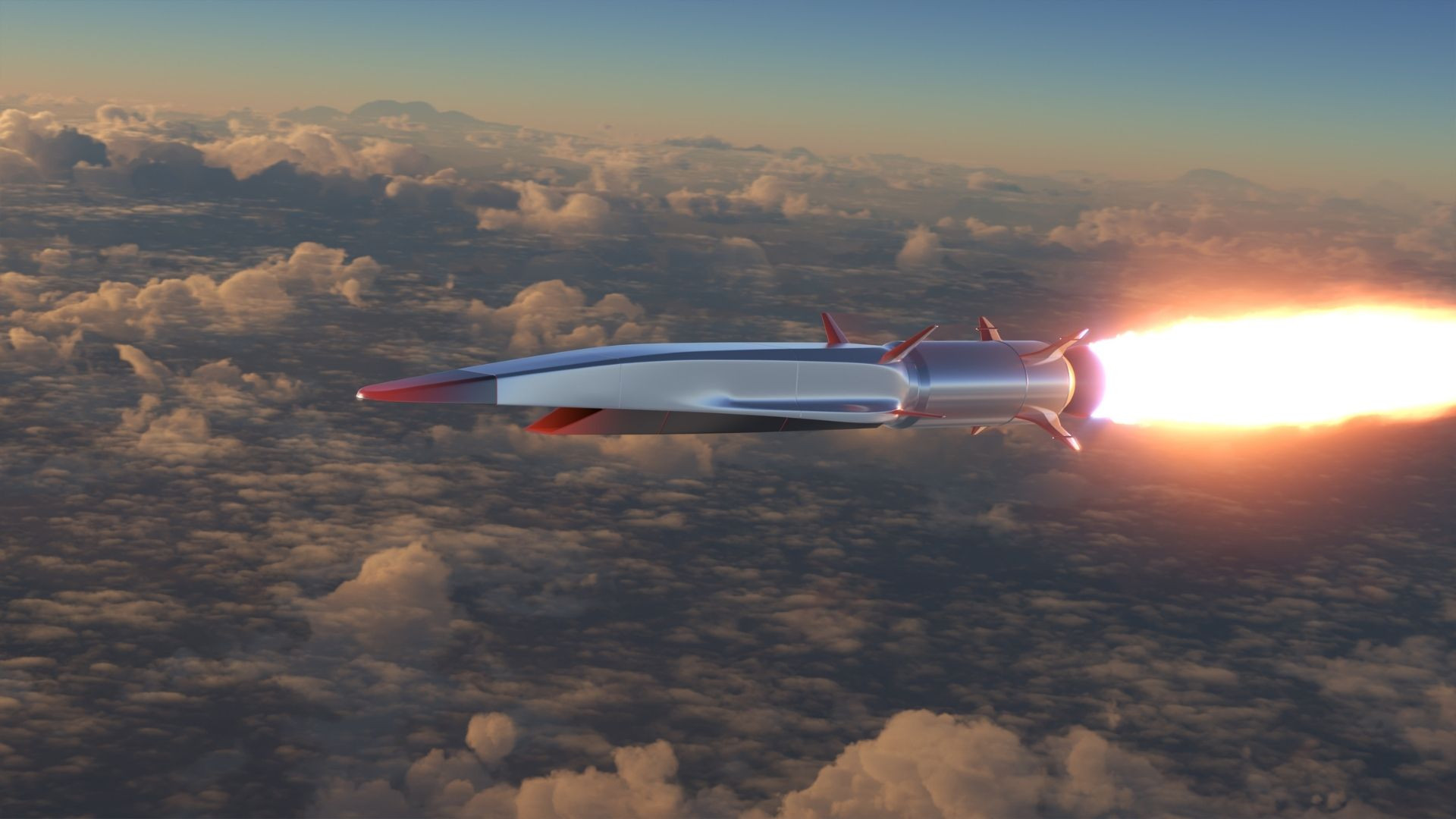
*Athanasios Tsakalos
How are the hypersonic vehicles protected from the extremely high temperatures (over 2,200°C) they develop when flying at speeds exceeding Mach 5? According to the RTX Technology Research Center, a division of RTX corporation (formerly Raytheon Technologies Corporation), the answer is to make them…sweat.
Hypersonic flights promise to revolutionize aeronautics to an unprecedented degree since the “breaking” of the sound barrier in 1947. However, it turns out that going from supersonic to hypersonic is a lot more challenging than going from subsonic to supersonic. One of the biggest challenges is the tremendous heat generated by a body flying in excess of five times the speed of sound.
Also read: Raytheon | A hypersonic missile takes flight
Hypersonic missiles can dart through the atmosphere faster than a mile per second. But at those speeds, the said systems get so hot that many materials would melt.
The problem
This means that the carefully designed lines of a hypersonic vehicle, especially its leading edges, will quickly round and distort, completely altering the aerodynamics of the vehicle. This is called ablation, which dulls the vehicle’s leading edge from a triangle to a trapezoid shape.
At these temperatures all but the most “exotic” of materials melt or become inoperable, so there is an increase in drag which ends up slowing the vehicle down, impacting how fast and far it can fly.
The obvious way to avoid this is to cool the outer skin of the vehicle. Unfortunately, with conventional systems, this means adding weight and complexity.
Heatproofing hypersonics
The RTX Technology Research Center has developed proof-of-concept hardware for a heat-proofing hypersonic vehicle that can keep its shape even under the aforementioned temperatures. Under a DARPA (Defence Advanced Research Projects Agency) contract, RTX is looking at cooling hypersonic craft using the same mechanism that humans use to beat heat – sweating.
Hence, to prevent the vehicle from overheating, researchers used a method called transpiration cooling, which mimics the way humans sweat. As such, they drilled thousands of pores into the test hardware and exposed it to extreme temperatures. A liquid inside then surfaced, keeping it within the tolerable temperature to help it maintain its shape.
Specifically, the concept is that the leading edges of a hypersonic vehicle would incorporate a network of micro-channels feeding a liquid to the surface of the skin in a manner similar to human sweat glands. As the liquid reaches the surface, it evaporates, carrying away heat. In this way, the craft can be kept cool enough to maintain its aerodynamics.
The solution
According to project team leader John Sharon at the RTX Technology Research Center, predictive modelling and advanced micro-machining were used to create a wedge-shaped test article about the size of a credit card. This was first exposed to a burner rig, which aims a torch fueled by natural gas and oxygen at the test article to mimic changes in temperature that would occur at hypersonic speeds.
Then they conducted more intricate testing at a facility that uses an electrical arc to heat and expand gases to high temperatures and speeds that more closely simulated hypersonic flight conditions.
The result
The tests offered preliminary proof that the concept would work, but Sharon said they’ll need more research and refinements before transpiration cooling is ready for use in hypersonic missiles. The remaining challenges include figuring out how to make the channels even smaller and determining whether their findings on a credit card-sized test article would scale to a full-sized hypersonic vehicle.
Should the technique prove successful, it may also be applicable to other problems, like protecting gas turbine blades.
Also read: Hypersonic weapons: The latest developments – VIDEO
READ MORE
NSPA | Awards first C-sUAS multinational contract in NATO’s history
The NATO Support and Procurement Agency (NSPA) has approved the first Counter-small UAS (C-sUAS) procurement framework agreement…
US Army | Receives new M10 Booker armored fighting vehicle
The US Army received the first M10 Booker light armored fighting vehicle during a formal ceremony on April 18, 2024, at the Aberdeen…
A reluctant alliance? A different approach to French – Serbian defence relations
It has only been a few months since Croatia started receiving the first of the Rafale fighter jets it ordered from France.
Agamemnon | The new Astute-class HMS nuclear submarine of the Royal Navy
The British Royal Navy has named the newly-built Astute-class nuclear-powered submarine HMS Agamemnon. Doing so, the…
NSPA | Awards first C-sUAS multinational contract in NATO’s history
The NATO Support and Procurement Agency (NSPA) has approved the first Counter-small UAS (C-sUAS) procurement framework agreement…
USA | Signs bill on military aid to Ukraine
US President Joe Biden has signed a bill providing Ukraine with billions of dollars in new aid for its war with Russia, marking a rare…
Armenian Genocide Remembrance Day
On this day, 109 years ago, the genocide of the Armenian people by the Ottoman Empire began, with April 24 being the day of…
United Kingdom | Increase in defence spending
Britain will gradually increase its defence spending to reach 2.5% of GDP by 2030, Prime Minister Rishi Sunak announced…